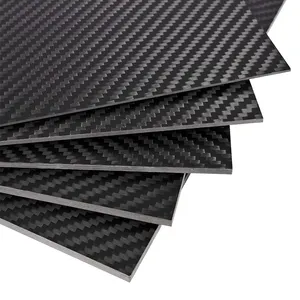
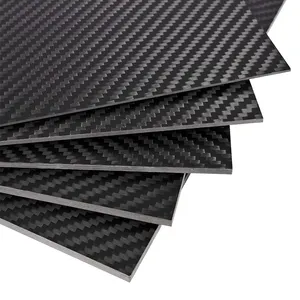
In an age where the strength-to-weight ratio of materials is a pivotal factor in innovation, carbon fiber sheets stand at the forefront of modern manufacturing. These marvels of material science, born from groundbreaking advancements in the 1960s, have revolutionized product development across industries. From aerospace to consumer electronics, the integration of carbon fiber sheets has not only enhanced performance but also redefined the boundaries of design and engineering. This article delves into the transformative impact of high-strength carbon fiber sheets, exploring their composition, types, applications, and the science that confers their unparalleled durability and strength.
The modern era of carbon fiber began with significant advancements in the 1960s when new manufacturing processes were developed. These methods allowed for the production of carbon fibers with enhanced strength and stiffness, which were not possible with earlier techniques. The introduction of polyacrylonitrile (PAN) as a precursor led to fibers containing a higher carbon content, marking a substantial improvement over previous versions. Patented processes further increased the strength of carbon fiber products, which began to be incorporated into high-performance applications such as jet engine components. Despite initial challenges, these developments laid the groundwork for the widespread use of carbon fiber in various industries.
By the 1970s, the collaboration and technology transfer between entities expanded the production capabilities of carbon fiber. This period saw the emergence of carbon fiber sheets with up to 95% carbon content, boasting superior tensile strength and modulus of elasticity. The advancements in manufacturing not only improved the quality but also reduced costs, facilitating the integration of carbon fiber sheets into a multitude of manufacturing applications. These improvements have established carbon fiber sheets as a preferred material for engineers and designers, seeking to leverage its exceptional properties in product development.
Carbon fiber sheets are composed of thin, strong crystalline filaments of carbon. These atoms are bonded together in long chains, creating a material with an exceptional strength-to-weight ratio. The manufacturing process involves several steps, starting with carbon-rich precursors like polyacrylonitrile (PAN), pitch, or rayon. These materials are spun into fibers, stabilized in an oxygen-free environment to prevent burning or shrinking, and then carbonized at temperatures between 1000 - 3000 degrees Celsius in an inert atmosphere. This process leaves almost pure carbon in a crystalline structure. The fibers are then given a surface treatment to enhance adhesion to matrix materials, such as epoxy resin, before being wound onto spools. The resulting carbon fiber sheets are not only strong and light but also stiff in tension and compression, making them ideal for a variety of structural applications.
Alibaba.com showcases a diverse range of carbon fiber sheets, tailored for various applications and industries. Among the offerings, you can find carbon fiber fabrics in different weaves such as plain, twill, and satin, available in 1K to 12K fiber counts. These sheets come in various weights, including options like 160g, 200g, 220g, and 240g per square meter, catering to specific strength and rigidity requirements.
The platform also lists specialized carbon fiber cloths with ultra-high conductivity, suitable for applications demanding superior electrical characteristics. For automotive enthusiasts and manufacturers, there are customized car components and performance parts, all utilizing the lightweight and durable nature of carbon fiber. These components are designed to fit a range of vehicle models, enhancing both aesthetics and performance.
In addition to the more traditional weaves, Alibaba.com provides innovative materials such as forged carbon fiber for curved product applications and hybrid fabrics that combine carbon fiber with aramid fibers for enhanced properties. For those seeking specific customization, there are suppliers offering chopped carbon fiber in various lengths, which can be used to reinforce or decorate car parts, or integrated into composite materials for industrial use.
Carbon fiber is a material that has found its way into a multitude of industries due to its exceptional strength-to-weight ratio. In the aerospace sector, it's utilized for components that demand high strength and low weight, contributing to fuel efficiency and overall performance enhancements. The sporting goods industry also leverages carbon fiber for its lightweight and durability characteristics, making it an ideal choice for equipment ranging from bicycles to tennis rackets.
The renewable energy sector has adopted carbon fiber in the production of wind turbine blades. The material's properties allow for longer, more durable blades that can withstand the stresses of constant operation. In the automotive industry, carbon fiber is used not only for high-performance vehicles but also increasingly in the design of more fuel-efficient consumer cars. Its application in these diverse fields underscores the versatility and transformative potential of carbon fiber sheets in modern manufacturing.
Carbon fiber sheets are renowned for their distinctive characteristics, which are derived from the unique properties of carbon fibers. These fibers, typically with diameters ranging from 5 to 10μm, consist of carbon atoms arranged in long, flat microcrystals that align parallel to the fiber axis. This structural alignment is crucial as it contributes to the high modulus and tenacity of the sheets.
The versatility of carbon fiber sheets is evident in their various forms, tailored through the manipulation of process parameters such as temperature and time. This allows for the production of fibers with specific desired traits, whether it be high modulus for stiffness or high tenacity for resistance to breakage.
In terms of composition, a carbon fiber yarn, or tow, includes several thousand fibers. For instance, a 12K tow contains 12,000 fibers. These tows are available in different sizes, ranging from 1K to 48K, and can be woven into carbon fiber fabrics. These fabrics are then typically used with a matrix, like epoxy or polyester resin, to create composite parts that boast exceptional strength-to-weight ratios.
Comparatively, carbon fiber sheets offer advantages over traditional materials such as metals, as indicated by data from various material databases. Their lightweight nature combined with their robustness makes them an ideal choice for applications demanding high performance with minimal weight burden.
Carbon fiber is renowned for its impressive strength-to-weight ratio, a key factor in its durability and engineering applications. The material is composed of carbon atoms bonded together in a crystalline formation, creating thin, strong filaments. These filaments are produced from materials like polyacrylonitrile (PAN), pitch, or rayon, which undergo a series of complex processes. Initially spun into long fibers, they are then stabilized in an oxygen-free environment to prevent burning or shrinking. Subsequently, the fibers are carbonized at extremely high temperatures in an inert atmosphere, which purges most non-carbon elements, leaving a structure that is nearly pure carbon.
The resulting carbon fibers are then given a surface treatment to enhance adhesion to matrix materials, such as epoxy resin, which supports the fibers in a stable matrix. This combination of carbon fibers and resin matrix creates a composite material that is not only lightweight but also exceptionally strong. The mechanical properties of carbon fiber composites depend on the fiber and resin's properties, fiber placement and orientation, and the fiber/resin ratio. These composites can achieve a stiffness of 10 msi and a strength of 90 ksi, showcasing their mechanical prowess.
Carbon fiber's durability is further evidenced by its lack of a yield strength, meaning it does not permanently deform under stress before reaching its ultimate tensile strength. This characteristic, along with the ability to create composites with tailored properties for specific applications, makes carbon fiber sheets a versatile and durable option in product development, offering significant advantages over traditional materials like steel or aluminum.
Carbon fiber is renowned for its exceptional qualities, which make it a superior material choice in various manufacturing sectors. The primary benefits of carbon fiber sheets include their significant weight reduction when compared to traditional materials such as steel, aluminum, wood, and plastics. This lightweight nature does not compromise strength; carbon fiber maintains a high strength-to-weight ratio, making it an ideal candidate for applications where both durability and reduced weight are critical. Additionally, carbon fiber is known for its stiffness, which surpasses that of conventional materials, providing enhanced structural integrity without adding bulk. Its low thermal expansion coefficient means that products made from carbon fiber sheets are less likely to deform under temperature variations, ensuring stability and performance in diverse environments. These advantages make carbon fiber sheets a compelling option for product development, offering a blend of lightweight, strength, and stability that is hard to match with other materials.
Choosing the right carbon fiber sheet for your product involves understanding the specific requirements of your application and the properties of different carbon fiber composites. Consider the strength and stiffness needed, which are determined by the fiber and resin combination. The local fiber density and orientation in the laminate dictate the magnitude and direction of strength and stiffness. For instance, a standard modulus plain weave carbon fiber in a 0/90 layup offers a certain balance of strength and flexibility.
Also, factor in the thermal expansion coefficient, especially if the product will be subjected to varying temperatures. Carbon fiber's low thermal expansion makes it ideal for applications requiring dimensional stability. The anisotropic nature of carbon fiber allows for tailoring the mechanical properties along specific axes, providing design flexibility. Analyze the loading and boundary conditions unique to your structure to ensure the chosen carbon fiber sheet meets the performance criteria.
Lastly, the manufacturing process itself can influence your choice. Techniques like wet layup, vacuum bagging, and CNC machining affect the final product's quality and suitability for your application. By carefully considering these factors, you can select a carbon fiber sheet that not only meets your design requirements but also enhances the overall performance of your product.
Carbon fiber sheets have emerged as a cornerstone in the realm of advanced materials, offering a unique combination of lightness, strength, and adaptability. Their journey from aerospace components to everyday products showcases a remarkable versatility, underpinned by the material's exceptional mechanical properties and thermal stability. The ability to tailor these sheets to meet specific engineering demands further cements their role in pushing the envelope of product development. As we have seen, the selection of the right carbon fiber sheet is a nuanced process, requiring a deep understanding of the application's needs and the material's capabilities. Embracing the advantages of carbon fiber sheets not only elevates the end product but also propels industries towards a more efficient, resilient, and innovative future. In conclusion, the strategic incorporation of carbon fiber sheets is not just a choice but a definitive step towards redefining the quality and performance of manufactured goods in the 21st century.