
TONGDA TDL-MB Needle punching machine non woven fabrics making machine
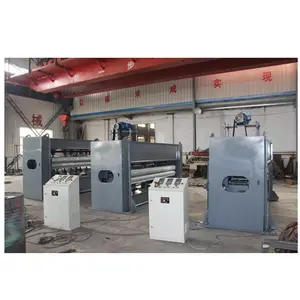
China Factory HOT Middle Speed Needle Punching Machine For Felt Making

Nonwoven Carpet Rugs Needle Punching Production Line Blanket Making Machine

Geotextile Nonwoven Machine Production Line Felt Blanket Carpet Needle Punching Non Woven Machine

ISO9001 ChangShu Hongyi needle punching carpet making machine for sale

Waste cloth recycling needle punch machine cloth recycled/felt needle punching machine

electrical heating oven thermal bonded needle punching machine for wadding production line

Nonwoven Jacquard carpet rug carpet base polyester exhibition color felt needle punching machine

jacquard carpet needle punching machine ( nonwoven machine )

Needle Punching Production Line,High Speed Needle Punching Machine,Non-Woven Fabric Machine

Low-speed non woven needle punching machine Mattress blanket felt carpet wool felt making machine

2021 New Design Non Woven Needle Punching Machine For Needle Punched Carpets Geotextile / Roofing / Insulation At Good Price

full automatic high speed needle punching machine for nonwoven fabric needle punching production line

Needle Punch production line pet needle punching nonwoven fabric making machine

Coir Fiber Mattress Needle Punching Felt Machine

china factory sell textile shoulder pad needle punching machine for geotextile carpet making machine weaving machines

Felt Opener Carding Machine Nonwoven Needle Punching Machine

HIGH SPEED NEEDLE PUNCHING MACHINE

professional manufacturer Needle Felt Needle Punching Machine For Blanket/nonwoven Felt Machine Line
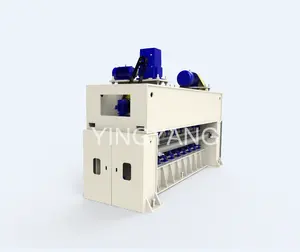
Non-woven Carpet Machinery Jacquard Carpets Making Machine Used Carpet Needle Punching Machine

Factory Wholesale Hot - selling cotton wool blankets needled production line non-woven fabric machines needle punching machine
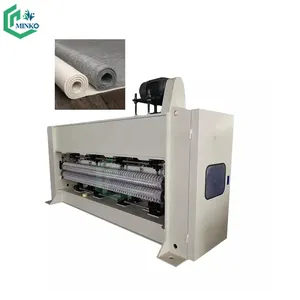
industrial needles punching machine used for wool felting machine non woven fabric making machine

Automatic rotary hydraulic needle metal steel hole cnc punching machine

CCD Automatic Double Needles Hole Punching Machine With CE Certification For Roll Materials

Metal stamping machine needle punching press machine for sale

High Sound Absorption Fire-proof nonwoven Polyester Fiber Acoustic Panel needle loom punching machine

AZX PET Spunbond Needle Punching Machine
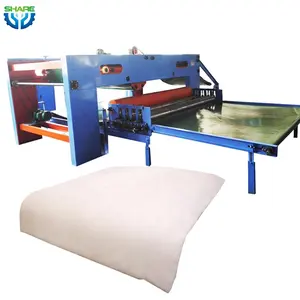
Vertical Cross Lapper for Product Line Needle Punching Machine
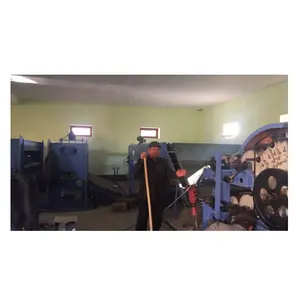
Nonwoven Needle Punching Wool Felt Making Machine Sheep Wool Felting and Wool Quilt Making Machine

Low-speed non woven needle punching machine Mattress blanket felt carpet wool felt making machine

Non woven ceramic fiber blanket needle punching production line felt making machine

High quality small power press pneumatic hole eyelet sheet metal needle rotary cnc punching machine for sale

Mc Washing Tank Hydraulic Machine For Punching And Shearing Needle Punching Machine Sieve Production Line Machines/Equipments

2024 Hot sell felt cotton air filter carpet making needleair filter carpet making needle punching machine

Thermo Bonded Padding Plant Pet Spunbond Nonwoven Needle Punching Machine

non woven needle punching machine non woven machine used non woven machine for sale
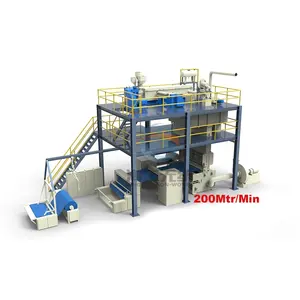
Geotextile Needle Punching Nonwoven Machine Carpet Textile Machine Used For All Nonwoven Machine

Fully Automatic Nonwoven Machine Needle Punching Carpet Production Line & Carpet Making Machine

PYS--Geotextile Needle Punching Nonwoven Machine Carpet Textile Machine Used For All Nonwoven Machine
