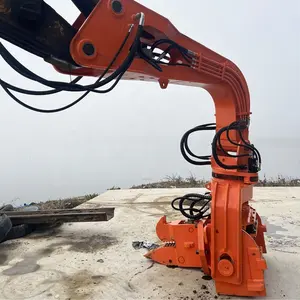
360 Degree Rotation K250 High Frequency Vibro Hammer Hydraulic Excavator Mounted Pile Driver Pile Drilling Machine

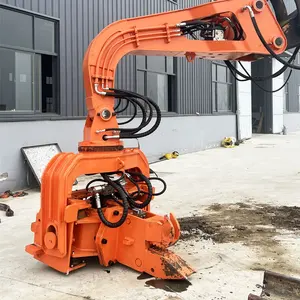
360 Degree Rotation K250 High Frequency Pile Driver Vibro Hammer Hydraulic Excavator Mounted Pile Drilling Machine

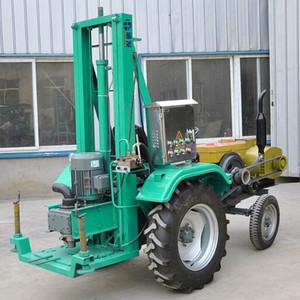
Embarking on the quest for a reliable deep well drilling machine requires a discerning eye for detail and a comprehensive understanding of the intricate technologies involved. Whether you're piercing through the earth's crust for water extraction or geological exploration, the right equipment is pivotal to success. This guide delves into the critical aspects of deep well drilling machines, from the mechanics of drilling and the various types available on Alibaba.com, to the essential features and considerations that ensure efficiency, safety, and longevity of your investment. Prepare to navigate the depths with confidence as we explore the key elements that define the best deep well drilling machinery for your needs.
Deep well drilling equipment is designed to create boreholes by rotating a string of drill rods and a bit against the formation. This process involves circulating a drilling fluid, typically water-based, to transport the drilled cuttings to the surface. There are different methods employed depending on the geological conditions, such as direct rotary drilling for cutting through formations with a circulating fluid, air rotary drilling in hard rock to estimate water production, and mud rotary drilling in unconsolidated sediments where the fluid stabilizes the formation.
The equipment includes powerful engines and transmissions, with rigs often powered by robust diesel engines and equipped with automatic transmission for reliability and versatility. Hydraulics play a crucial role, with rigs featuring direct-drive hydraulic feed systems for enhanced safety and power, eliminating the need for cables or chains. Leveling jacks ensure the rig is perfectly straight for accurate drilling, while drill rods work in increments, penetrating the overburden to reach aquifers within the bedrock.
Drill bits are selected based on the material encountered underground, with options like diamond bits for hard formations, drag bits for hard clays and soft shale, and tricone bits for gravel. The mud manager and mud pump are essential for separating cuttings from the water and maintaining the flow of drilling fluid. The well casing is installed to prevent contamination of the water supply by overburden. For areas with low water production, bucket rigs with a cutting and lifting mechanism are used.
Alibaba.com showcases a diverse range of deep well drilling machines designed to cater to various drilling depths and environments. Among the selection, crawler-mounted drilling rigs are prominent, offering enhanced mobility and stability, suitable for drilling up to 200 meters. For agricultural applications, tractor-mounted hydraulic rigs with optional coring bits are available, emphasizing versatility and ease of use. Portable drilling rigs are also featured, providing a compact solution for water well drilling in remote locations.
The platform lists both pneumatic and hydraulic drilling rigs, with the hydraulic variants being favored for their efficient power transmission and smoother operation. These rigs can reach depths from 100 meters to beyond 300 meters, suitable for both small-scale and industrial drilling projects. Additionally, electric and diesel engine options are presented, giving buyers the flexibility to choose based on their power preferences and site accessibility.
For deeper drilling requirements, heavy-duty rigs capable of reaching depths of 500 meters or more are also available. These machines are equipped with robust drilling technologies, such as DTH (Down-The-Hole) and rotary drilling, ensuring efficient penetration through various substrata. The inclusion of air compressors in some models enhances drilling speed and efficiency, particularly in challenging geological conditions.
When selecting a deep well drilling machine, it's crucial to consider the mud pump's capabilities, as it is a pivotal component in the drilling process. A robust mud pump enhances job efficiency by effectively clearing the hole of cuttings. It's advisable to avoid underpowered engines for the mud pump, as they can lead to increased wear and more frequent servicing. The engines should match the scale of drilling projects, with more powerful options available for deeper drilling requirements.
The construction of the drill is equally important. Drills should have a heavy-duty welded steel frame to withstand repetitive use and harsh environments. Inferior quality can lead to structural weaknesses, such as bending or corrosion, which compromise the drill's longevity. Opt for drill pipes and connections made of heat-treated alloy steel, especially for demanding drilling tasks, to reduce the need for replacements.
User-friendly design features that facilitate ease of operation and maintenance can also be a deciding factor. Features such as accessible greasing points and tension adjustment for the drill chain are essential for maintaining the drill's condition and extending its lifespan. Additionally, consider the availability of various drill bit types to ensure compatibility with the soil conditions and maximize the drill's performance.
Drill bits are integral components of deep well drilling machines, especially when it comes to drilling through various substrates. The materials used to manufacture drill bits are crucial, as they determine the bit's durability and effectiveness. Common materials include high-speed steel (HSS), cobalt, and carbide, which are selected based on the hardness of the material to be drilled. HSS bits are versatile and used for general drilling purposes, while cobalt bits are an upgrade for tougher materials due to their superior heat resistance. Carbide-tipped bits are the hardest and are reserved for the most demanding drilling tasks, where precision and longevity are paramount.
The design of the drill bit, particularly the flute design, point angles, and lengths, also plays a significant role in deep well drilling. Flutes are grooves on the drill bit that facilitate the removal of debris, and their design affects the efficiency of material removal. Point angles, such as the common 118 degrees for softer materials and 135 degrees for harder substrates, influence the bit's starting precision and wear rate. Shorter drill bits are recommended for their rigidity and accuracy, which are essential in deep well drilling operations where precision is key.
Coatings on drill bits, such as black oxide, titanium nitride, or diamond powder, enhance the performance and lifespan of the bits. These coatings serve to protect the bit from wear and heat buildup, which is particularly important in the high-friction environment of deep well drilling. The right combination of material, design, and coating ensures that the drill bit can handle the specific requirements of deep well drilling, contributing to the overall efficiency and safety of the drilling operation.
Pneumatic and hydraulic systems represent two distinct approaches to drilling, each with its own set of benefits. Pneumatic drills operate on compressed air, making them suitable for lower to medium production requirements. They are known for their simplicity in maintenance and operation. On the other hand, hydraulic drills offer more control over drilling parameters, such as rotation speed and percussion, which is crucial for avoiding deviations in longer drill holes. This makes hydraulic systems preferable for high-demand drilling tasks or when starting a new project.
Hydraulic systems stand out in their ability to adjust to varying drilling conditions, providing more power and efficiency compared to their pneumatic counterparts. They are particularly beneficial when developing new areas or when there is a need to ramp up production. The flexibility in controlling the working parameters of hydraulic drills translates into more precise and efficient drilling operations, especially in challenging drilling environments.
Investing in a quality deep well drilling machine ensures efficiency and longevity, which translates into a better return on investment. Key components such as the mud pump and the construction of the drill itself are critical. A robust mud pump is essential for clearing the hole of cuttings, which can otherwise hinder the drilling process. The construction of the drill, particularly the materials used, like heavy-duty welded steel frames and heat-treated alloy steel for drill pipes, ensures durability and fewer replacements over time.
The engines powering the mud pump and drill should be appropriately sized for the job to prevent excessive wear and the need for frequent servicing. For deep well drilling, machines with larger engines and mud pumps capable of reaching greater depths are preferable. These machines are designed to handle more demanding environments, providing optimal performance and reducing the likelihood of downtime due to equipment failure.
Furthermore, the design of the drill should support ease of operation and maintenance, with features like conveniently located greasing points and accessible tension adjustments for the drill chain. This user-friendly design not only saves time but also extends the life of the machine. Additionally, using the correct drill bit for the soil conditions and adding accessories like down-the-hole hammers for hard rock formations can significantly enhance the drill's performance and longevity.
Ensuring the safety and proper maintenance of deep well drilling machines is paramount to prevent accidents and extend the lifespan of the equipment. A qualified individual with the right training should always conduct maintenance checks. Daily and throughout the day, emergency shutdown systems need to be verified for proper function to avoid accidents.
Adherence to a maintenance checklist is crucial for organization and accountability. This should include a daily inspection form, signed off by the responsible parties, to maintain a record of any issues and actions taken. It's also essential to have the owner’s manual readily available on-site for reference.
Personal protective equipment (PPE) is non-negotiable and must be worn at all times to safeguard against job-related hazards. Regular care of the rig’s components, such as oil, stop switches, and cables, is necessary, and greasing the machine should be part of the preventive maintenance routine.
Maintenance should never be performed while the rig is operational to avoid safety risks. Keeping the rig clean not only reflects professionalism but also is part of maintaining the equipment in good working order. Despite all precautions, unexpected issues can arise, so the goal is to minimize these occurrences through diligent safety and maintenance practices.
Navigating Alibaba.com for the best deals on deep well drilling machines involves understanding the variety of options available. On the platform, you can find a range of drilling equipment, from small rigs suitable for water well borehole drilling to large-scale machinery capable of reaching depths of 450m and beyond. When searching, consider the depth requirements of your project, as machines are listed with their maximum drilling capacities, such as 100m, 200m, and up to 800m.
Alibaba.com also offers ready-to-ship products, which can be an advantage if you're looking to expedite the procurement process. These listings often include essential specifications like the type of power source – whether it's a gasoline hydraulic wheel borehole drilling machine or a crawler diesel engine truck well rig. The site's filters allow you to sort by machinery type, such as portable rigs, tractor-mounted units, or truck-mounted rigs, enabling you to match the equipment to the terrain and drilling conditions you expect to encounter.
For specialized drilling needs, Alibaba.com features equipment like deep well oil drilling rigs with specific components for cementing operations. It's important to assess the technical specifications and compare the features of different models. Look for details on the drilling rig's capabilities, such as soil testing, rock coring, or exploration drilling. By carefully reviewing the product descriptions and leveraging Alibaba's comparison tools, you can make an informed decision tailored to your deep well drilling requirements.
In the realm of deep well drilling, the choice of machinery is not just a purchase—it's an investment in efficiency, safety, and project success. The guide has traversed through the essential considerations, from the robustness of mud pumps and the resilience of drill construction to the precision of drill bits and the power of hydraulic systems. It's clear that quality equipment from Alibaba.com, tailored to the specific demands of your drilling project, can significantly enhance performance and reduce downtime. Safety and maintenance practices stand as non-negotiable pillars that ensure the longevity and reliability of your machinery. As you navigate Alibaba.com's extensive offerings, remember that the best deals align with your project's depth requirements, operational conditions, and technical specifications. With this comprehensive buyer's guide, you're now equipped to make an informed decision that will yield dividends in the form of successful, safe, and sustainable deep well drilling operations.